Evolution in engine building: Hatz H-series Applicationizer
30 October 2019
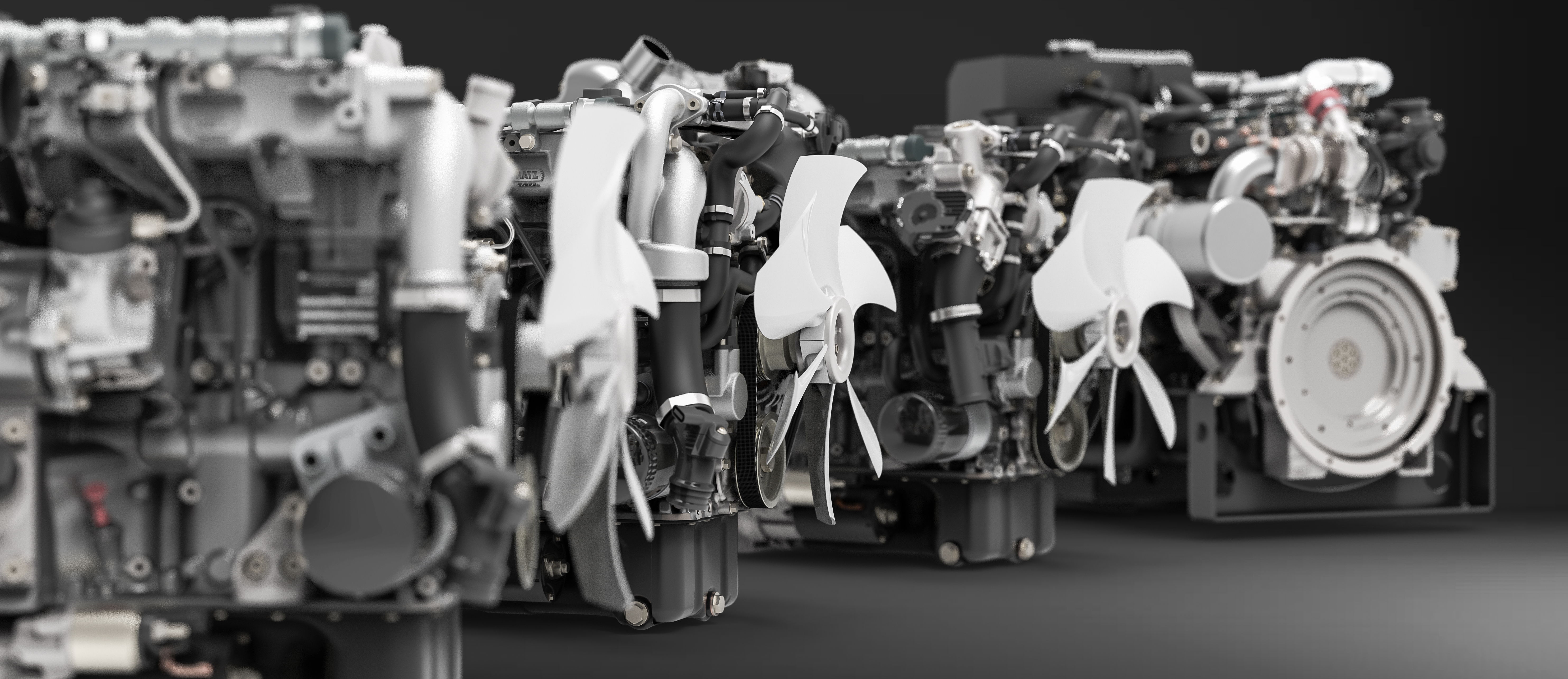
Industrial diesel engines have been used for decades in all kinds of machinery. And they do their work well. But the time came to rethink the classic industrial diesel engine from the ground up. This was because the partial developments to existing engine platforms that commonly occur in industry could no longer do justice to the great challenges and demands in the long term. Hatz took on this task and redefined industrial diesel engines for small and medium-sized machines with its Hatz H-series.
The Hatz H-series engines – the Hatz Applicationizers – are a product of the company's long-standing expertise and innovativeness. Clearly fundamental inventions, such as the flat-seat injection nozzle of 1926, which lastingly influenced developments in diesel technology, or the first industrial diesel engine made out of aluminium in 1958, something that only became an industry-wide standard many years later, mark only two of Hatz's many great moments. The engine specialist has once again set a milestone in innovation and development industry-wide with the H-series three- and four-cylinder diesel engines.
Why the Applicationizer? Because the Hatz engines of the H-series constitute a completely new diesel drive generation, which elevates off-highway applications – i.e. machines that are not driven on the road – to the next evolutionary level. To mention just a few of their advantages, the three- and four-cylinder diesel engines boast impressive features, such as high specific power, efficiency and torque with less displacement, lower weight, smaller size, lower fuel consumption and lower emissions. The new engine class was achieved by adhering to a consistently implemented downsizing principle combined with first-class components. These include sturdy, highly effective turbochargers and Bosch's special off-highway common rail injection system. Other components, for example from Mann+Hummel, Mahle, Behr and Kolbenschmidt/Pierburg, are top-quality supplements to the Hatz engine design.
Photo: Applicationizer: The Hatz H-series engine range is designed for a very wide variety of applications.
Diversity of variations for versatile deployment
The Applicationizer's diversity of variations is based on one engine family with two platforms, the three- and four cylinder H-series. Both the three- as well as the four-cylinder engines are based on the same basic design with a thin-wall cast cylinder crankcase, a die-cast aluminium cylinder head with cross-flow cooling and the OHV two-valve concept with a decentralized injector position.
The Hatz product range includes various derivatives and development levels of the two basic engines in order to provide the ideal engine for almost every machine type. This gives machine manufacturers a great deal of choice when it comes to power versions, emission classes or engines with special casings for weather protection and noise insulation. A total of eight engine variations are available, which drive machines with up to 64 kW and the most innovative technology.
llustration: Hatz Applicationizer: the generic term for the application flexibility and worldwide deployment of different engine models of the H-series, each with nominal ratings, equipment (CR = Common Rail, T = Turbocharger, IC = Intercooler, cEGR = cooled Exhaust Gas Recirculation, DOC = Diesel Oxidation Catalyst, DPF = Diesel Particulate Filter) and emission classes
The superlative can be found in the details: lowest emissions
Apart from complying with EU Directive 2016/1628 (EU Stage V), in force since 2019, the requirements of the US EPA Tier 4 final were naturally also included in the engine redesign. Several aspects were decisive in this regard. One of them was the very low vibration level of the drive, which was realized despite deliberately dispensing with a balancer shaft. As a result, it was not only possible to keep the size and weight down, but also to minimize friction losses along with the accompanying fuel consumption and associated CO2 emissions.
The iHACS (intelligent Hatz Advanced Combustion Strategy) is crucial in guaranteeing optimal raw emissions. This involves special combustion chamber geometry, combined with individually defined injection patterns, gas exchange and optimized exhaust gas recirculation. Other considerable advantages to the iHACS combustion procedure include particulate filter adaptation. The highly efficient combustion procedure with its low fuel requirements promotes extremely low soot input while the minimal oil consumption leads to reduced ash input into the filter. On the one hand, this facilitates lengthy intervals between the active regeneration cycles with little influence on overall fuel consumption, while on the other hand realizing very long service lives before ash scrubbing becomes necessary. Together, these advantages cut overall operating costs.
Moreover, the tried-and-tested two-level cooling of the exhaust gas recirculation (EGR) with liquid-cooled EGR valve, combined with valve timing that dispenses with dirt-prone hot-film air flow sensors ensures stable emissions in the long term. But it would not be Hatz if the engineers had failed to take it a step further from the get-go. This is because the engine series has already been prepared for operation with paraffinic fuels according to EN 15940 for "zero carbon" operation.
Power aplenty in compact design
The power class of the entire H-series is distinguished by a high supercharging degree with simultaneously simple engine design. This is achieved with the help of a mechanical wastegate turbocharger and intercooler. The engine's highly compact design is one result of this technology. Thanks to the engines' enormous power and high torque, machine manufacturers can use the Hatz H-series in machines normally fitted with higher displacement class systems. The turbocharged three-cylinder 3H50TICD engine with intercooler and 1.5-litre displacement is proof that more than enough power is available. It already reaches its high torque of 200 Nm at 1700 rpm, which in many cases even exceeds the torque of older 56 kW engines. In addition, there are H-series versions under 19 kW, without an intercooler, which already deliver a very high torque of 130 Nm at 1300 rpm and as a result encroach on the former 19–37 kW class. This means torque-intensive applications, such as hydraulic hoisting, are no problem. In addition, noise emissions have been slashed compared to conventional engine solutions without a turbocharger, thanks to the low speed of the Hatz engine.
Illustration: Nominal rated values of the Hatz 3H50TIC/4H50TICD – torque and power
Small size of the engine creates space and reduces weight
A special design challenge for Hatz was retaining the H-series' compact dimensions while integrating additional indispensable components, such as the diesel particulate filter (DPF). This massively reduces the construction space problems in machines for manufacturers due to the conversion to Stage V. The DPF in particular plays a decisive role in an engine's space requirements. Consisting of a cordierite DOC and silicon carbide DPF, the DPF was placed at the front of the engine contour and as a result only extends the engine in the direction of the pto above the flywheel housing. Furthermore, the optional integration of a glow device in the inlet housing to the DOC to raise the exhaust gas temperature during the active regeneration phase, combined with a more powerful 150 ampere alternator, was realized without additional construction space requirements. Another decisive factor was the development of far more compact electronic components, which are grouped in the plug-and-play solution of the Hatz OPU (Open Power Unit) in the central electric assembly.
Yet another important achievement of the H-series' design is the particulate filter concept. It permits maximum flexibility with minimal space requirements. The modular design with a wide range of exhaust outlets, engine or chassis mounting and optional horizontal, vertical or inclined placement facilitates versatile, space-saving installation.
Hatz DPF regeneration: an industry-wide innovation
DPF regeneration or the regeneration strategy for the particulate filter system consists of a complex interplay of technical necessities and user-friendliness for the machine operator. Hatz adopted a completely new approach here. The goal was to maximize the range of use and reliability in every conceivable installation scenario. Hatz implemented novel thermal management via demand-actuated adjustment of the exhaust gas recirculation via the adjustment of the throttle valve, late displacement of the combustion and additional application of late to very late, but still torque-generating injection, with simultaneous realization of a very low light-off temperature on the DOC. In addition, with optional additional heating at the the DOC inlet, an increase in the exhaust gas temperature is possible via the internal engine load boost and external energy supply. This makes an individual reaction to all load profiles possible. Moreover, additional dosing of uncombusted fuel from split, very late injection facilitates temperature control during the active regeneration phase. Another achievement is the automatic shut-down of one (3H50TICD) or two (4H50TICD) cylinders during standstill regeneration. This reduces the exhaust gas flow and increases the temperature level during the temperature control phase. This is the first use by Hatz of automatic cylinder shut-down in industrial diesel engines in this power class.
Hatz Applicationizer at a glance
The design of the Hatz H-series engine platform is distinguished by its durability, power, compact size and great maintenance friendliness. Innovations like the iHACS combustion procedure ensure observance of the emission thresholds; with an additional diesel particulate filter, stricter limits, such as the EU Stage V Regulation, can be observed – with identical power characteristics and scarcely changed size. This is all to the benefit of the machinery manufacturer and operator: the range of three- and four-cylinder models has been designed for a wide variety of uses and provides a drive for almost every scenario and market.
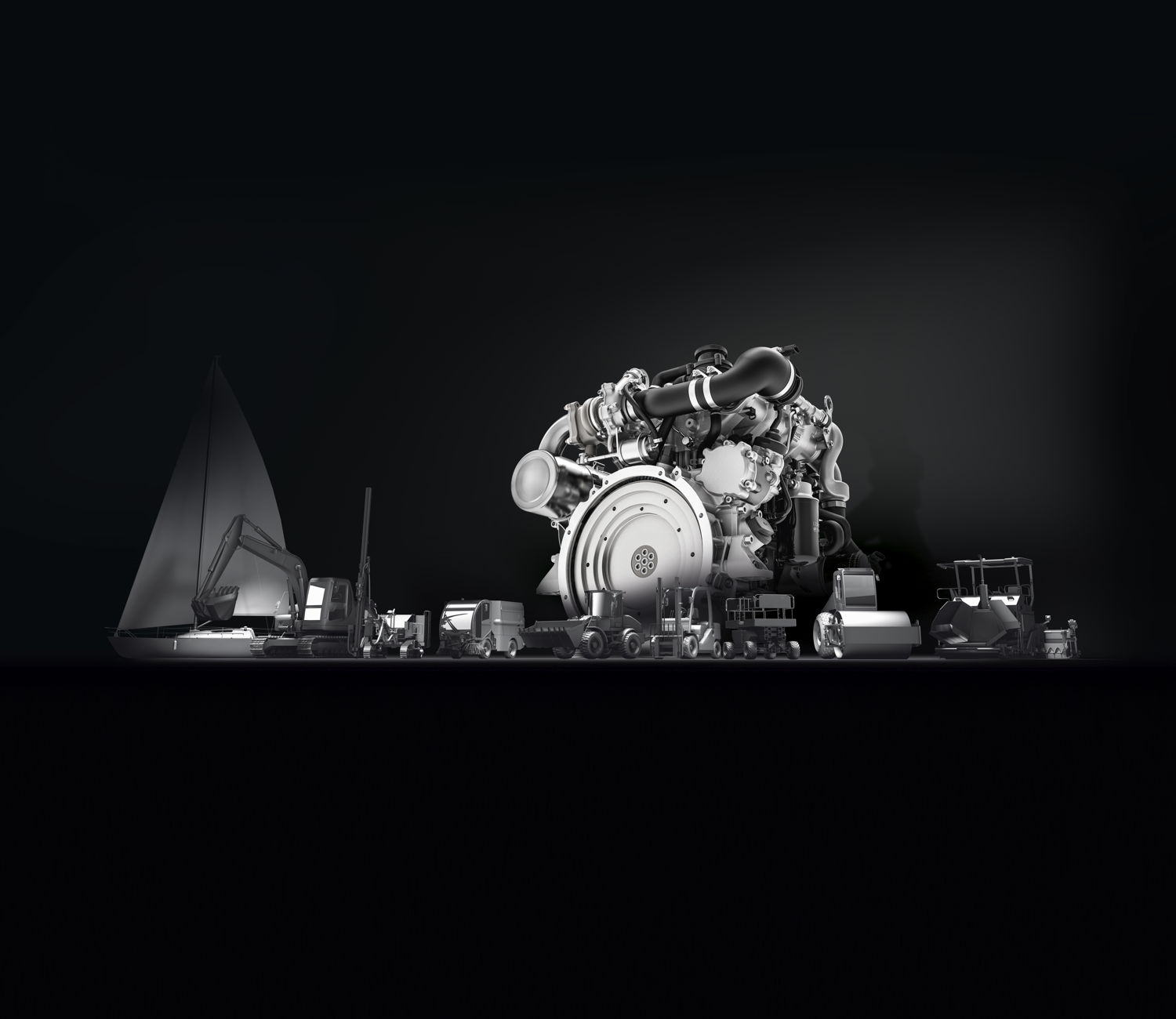
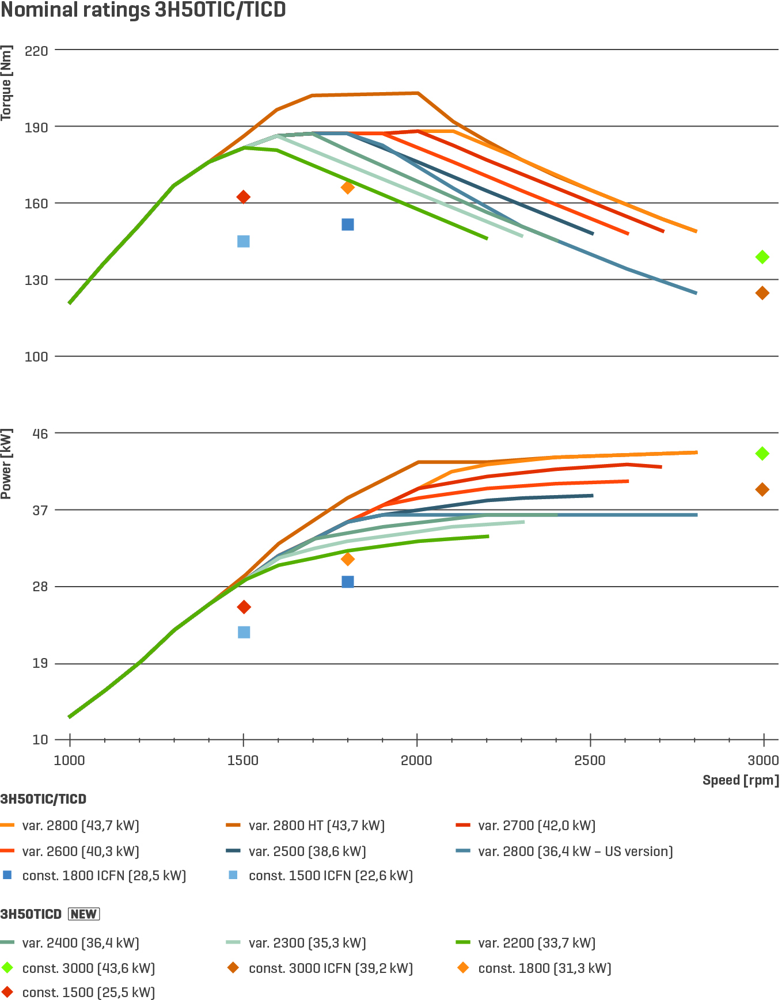